Formula SAE Michigan 2014
May 17, 2014
It’s finally come and gone, the event we’ve worked so hard to get to, Formula SAE Michigan 2014!
Early on the 13th of May we got packed and ready to hit the road. Our journey from Carleton University in Ottawa, to the Michigan International Speedway in Brooklyn, Michigan would cover 1000 kilometers of road, and our convoy of cube vans and cars of all shapes in sizes was ready. Packed away were all of our tools, our brand new car, and everything we could possibly need for our four days of 94 octane fuelled fun.

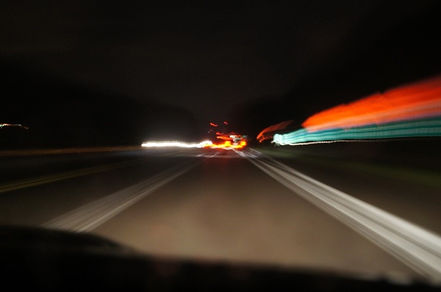
Our day of travel was filled with a few stops for food, fuel, and to pick up a few team members who lived along the way. Our journey through the flattest section of Ontario was fairly uneventful, aside from the brief thunderstorm, our sighting of a campervan with its awning out driving down the highway, and some humorous radio conversation. Our crossing at the border was relatively swift (for a team with a no-name cube van and a dozen international students) and before we knew it we were at our hotel in Jackson, Michigan.
The next morning we dragged ourselves out of bed and hit the road for the track. We got there just in time to get in line behind every other truck imaginable. Everything from USF’s school bus to hydro utility trucks borrowed from provincial power companies. We were greeted by this amazing sign.

After waiting with the crowd for what felt like an eternity we entered the pits and could begin to prep for all of our upcoming events. First on the list; unpack the truck, set-up the tents, and get in line with driver gear and rain tires for inspection. Once inspected were given a ticket for technical inspection of our car and the fun began.
With the rain staring to fall we roll the RR14 fresh out of the truck and into the inspection garages. For the first time in a long time our technical inspection is smooth sailing.

The judges asked us to change the placement of our fuel filler neck, and to add a quick zip tie or two to secure our clutch cable line and flex hose brake lines. But these were all issues we could fix then and there. Most important on their list; move our rear brake hardline another inch away from our chain and driveline. This unfortunately meant we needed to redo the entire line, but the judge granted us a passing grade (and the all-important sticker) under the condition that when they come by to check on the car the next day, the line would be replaced. Needless to say we thanked them kindly, rolled back to our pit, and had the new line installed before they had even finished their next inspection.
We also scored a few smiles from the judges during our first egress inspection. Our driver Mackenzie was out of the cockpit, with two feet on the ground faster than anyone thought was possible. The judge hadn’t even started his stopwatch. He smiled, told us he missed it, and asked Mack to get back in and do it again. The second time the clock was running and Mack was out in just over three seconds, well within the mandated five second maximum.
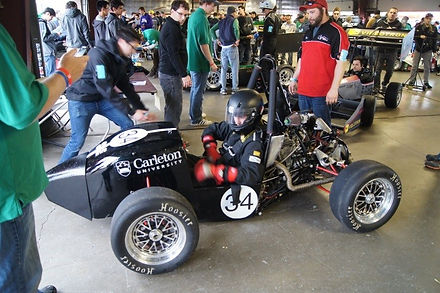

After our technical inspections we headed over to the dynamic tests; tilt, noise, and brake tests. Each test is necessary for our involvement in the dynamic driving events, and each presents its own challenges.


Our time on the tilt test table was quick and simple, no issues whatsoever. Our loud performance for the judges at the noise test area was enjoyable but nerve racking. The distinct lumpy sound of our single cylinder 250cc Yamaha catches the attention of other teams running 600cc four cylinders, but we like it that way. We record a 109 Db sound level at the test, just 1 Db under the 110 Db limit that would have kept us out of competition. Finally we completed the brake test. Our worn out slicks had been used multiple times before competition for the same purpose and the little bit of extra rain and cold air only helped us along. After a few times through the brake test box we had locked up all four tires, and finally got our last inspection sticker. Dynamic Events here we come!
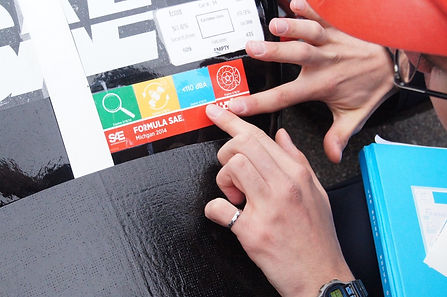
On the second day of competition in Michigan our emphasis was on the static events of the competition. We went through our marketing presentation, where we pitch our design and potential marketing plan to a group of experts in the automotive field. The entire Formula SAE competition is designed around building a production run of race cars for use on small racetracks or a formula race series. The marketing event is our opportunity to explain how we would sell our design, who we would sell it to, and what we think they would use it for. It’s almost like a student race car version of Dragon’s Den or shark tank.
The marketing presentation goes hand in hand with the cost analysis part of the competition. Each competition requires teams to submit a full report on the cost of their final design. Manufacturing costs for each component are calculated based on the average production cost of 1000 full cars. Teams who can properly document all aspects of their car in a realistic manner, and can validate their choice of each manufacturing method will score well in this event, and the best teams typically spend years refining their report. This year we placed 35th out of 120 teams, a great achievement.
Our final static event is the design competition. The entire team comes dressed in uniform, reports in hand, and ready to go. Here we meet a selection of automotive engineering experts and get our chance to tell them what makes our designs, and the RR14 special. We’ve spent years preparing for this moment. And we had better take this opportunity to tell them about every last bit of it. Our most impressive bits this year:
-
Custom carbon fibre impact attenuator. This crash structure is impressively lightweight and can stop the car in an impact smoothly and safely, with a peak G load of half the mandated maximum.
-
Axially compounded torsion spring suspension. We went away from coil over springs and designed and manufactured our own custom torsion springs in house.
-
Custom 3-D printed air intake. The intake pulses from a single cylinder make intake geometry and smooth intake flow tricky to perfect, but we put a lot of effort into it.
-
Motec ECU and SPDI Spark engine controls. This year we aimed for both an increase in power and efficiency. To do this we worked to make our own engine maps, and combined them with a new plasma spark system.
-
Carbon Fibre side impact structures. We removed a few mandatory tubes from our frame and increased our frame strength by replacing them with carbon fibre panels.

Overall our design event went well, the judges asked us questions until we couldn’t answer anymore, then they took a seat and thanked us for coming, we thanked them and rolled out of the garage to the pits again. We placed 38th out of 120 teams in the design competition, a well-deserved position. Next year we know we can take what we’ve learned and break into the top twenty.

Our second day ends with some time in the practice area. A good opportunity for the drivers to get used to the smooth pavement of the Michigan International Speedway, and a good opportunity to make sure everything is working as we want it to. We typically test in a very bumpy parking lot on campus, so the track here is something we get to enjoy once a year.
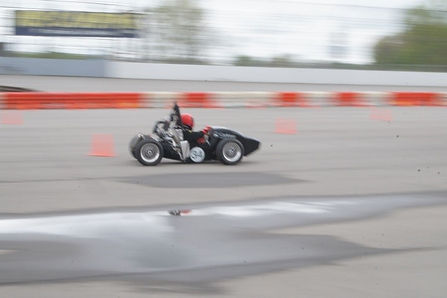
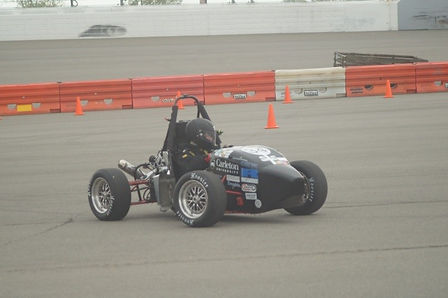
We were content with our progress. This year is the fastest we have ever gotten through our technical inspections and some of our best results in the static events. We finished our practice runs with lots of fuel still left in our tank and packed up for the night. We left the track early and headed off to get food. Sprits were high and we were all looking forward to the next day and the dynamic events; Skid-pad, Acceleration, Autocross, and Endurance.


No matter where we go, we usually fill up all of the tables.
The next morning started bright and early at the track, the risk of overnight frost and rain in the morning meant that we slept with our rain tires to keep them warm (a rather odd recommendation from our teams’ equivalent to Yoda – Mr. Glen Clarke). Our day began by starting up the car in the pits and checking everything over in the engine maps just one more time. Being a Canadian team that tests during the winter, we’re used to very cold “cold-starts” on our engine, (we even have a separate map for that). Other teams weren’t so lucky, and we happily loaned out our battery charger when our neighbours ran out of juice trying to crank things over.
Next we performed one final alignment and corner balance check on the car, and then we were off to the races!

Our first dynamic event was the skid-pad, a perfect figure of eight. Drivers enter the figure, drive two laps to the left, two laps to the right and then exit. The team with the fastest time average for one loop from each side earns the most points. The RR14’s relatively low power output and even weight distribution mean skid-pad doesn’t pose too many problems. Our centre of gravity is very low without an aero package, and our stiff torsion springs keep the car nice and flat. We placed 47th in the skid-pad. Well above lots of our toughest competition, but we certainly have room for improvement.

Next up, acceleration! The acceleration event is our known weakness. Our small 250cc engine is perfect for events like skid-pad and endurance. It is lightweight and sips fuel compared to the CBR 600 that is so common amongst our competitors, but it does lack the outright power needed for acceleration. We placed 75th in acceleration. Our time was well off the pace set by some other cars, but our designs for next year already show the potential to put us at the top of the pack.
After acceleration was autocross, the event that the RR14 is meant for. The RR14 places 67th in autocross, a great improvement over our recent competition results. From here on out we know the RR14 will shine.

Our final dynamic event was the endurance race, a 22 km session in which cars are pushed to their breaking point. In North American competitions less than half of the cars that enter the endurance track finish the event. This year in Michigan the success rate was low, with only 46 cars completing the race. Cars that do complete the endurance race are also eligible for the fuel efficiency competition. Given our aim to make the RR14 as efficient as possible, we knew that we had to finish the endurance race. Prior to competition we ran the car through two endurance test runs to be confident in our design, and sure enough the work paid off. We finished the endurance with no issues on the car and placed 34th overall. Our completion in the event and all of our work tuning our engine also earned us second in fuel efficiency. Both amazing results for us, we couldn’t have been happier.
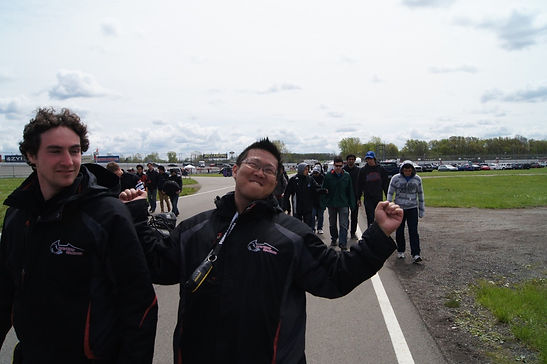
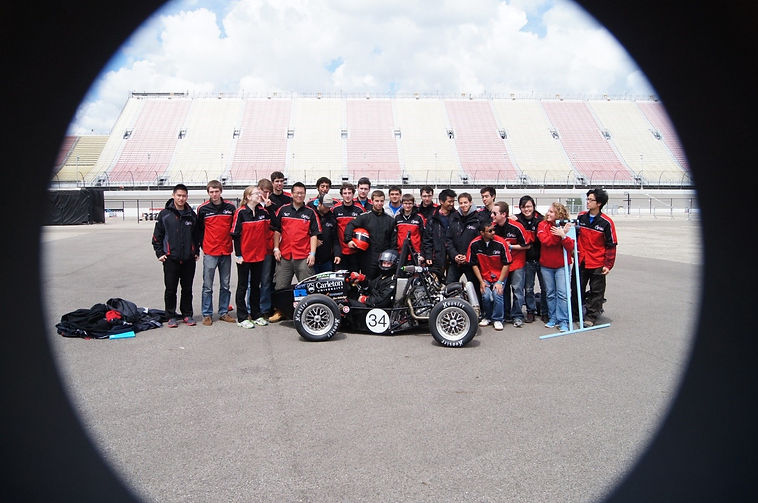
Time to enjoy the sights and sounds as the rest of the teams take their shot at the endurance track.
The entire event wraps up with an award ceremony, our engine management work and fuel efficient work earn us second place in the FEV Powertrain Development Competition, second place in fuel efficiency, and 41st place overall out of 109 teams.


Next up, we are headed to Formula North, a little bit closer to home….. but we still have a long journey on the road ahead of us.

Our most popular pose all week…….. Cube vans aren’t known for being aerodynamic, or efficient, but they can haul a lot of stuff…