December Manufacturing Update
December 8, 2014
Manufacturing has begun on the RR15 and RR15E frames. This year we have placed a strong focus on manufacturing reliable jigs for our frame manufacturing process. In the past, we’ve only had to manufacture one frame for one car every year. In this case a jig is always nice to have to keep frames tubes in place but it isn’t entirely necessary.
In 2012-2013 our old team lead Kenneth Chow welded our entire frame without a jig, and although the frame had its own unique character (slight errors) it was within an acceptable tolerance and was a reliable platform for many years.
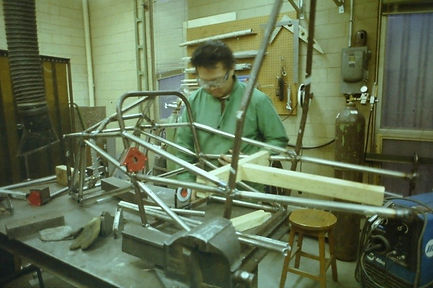

In 2013-2014 we worked to build a jig that was reliably stiff and could place our suspensions mounts with a higher level of accuracy. The jig was a flat plate arrangement that rested on a flat welding table for support. This jig was a good step in the right direction, but it was bulky and the frame had to be removed from it to finish weld most of our tube joints. This is less than ideal so we knew we could improve our set-up in the future.



For 2014-2015 we have worked to build an automotive rotisserie. This rotisserie jig aims to improve two main areas of our frame manufacturing. 1st – the jig is meant to ensure that the two frames and subframes we are manufacturing will have identical suspension and drivetrain mounting points. 2nd – the jig is designed to allow for welding access to all points of the frame, without having to remove the frame from its fixture.
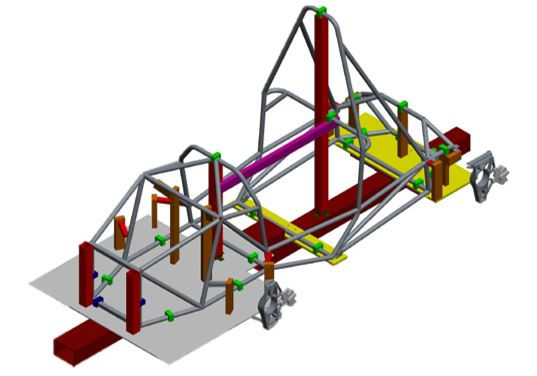


Our first frame was completed on December 6th, ready for suspension arms driver controls and steering systems to be mounted. Our first frame is dedicated to our combustion car, the RR15. The second frame is well under way and will be dedicated to the RR15E electric platform.
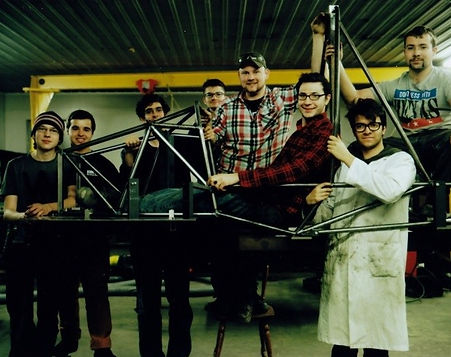

Next up, rolling chassis!